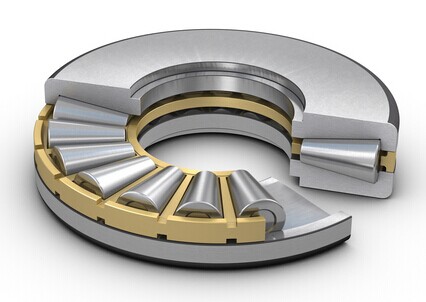
Gothenburg, Sweden, 5 May, 2016: In the oil and gas industry, reliability is key to success. Unexpected downtime due to machinery or component failure results in massive cost both onshore and offshore sectors.
US regulations require that equipment used in the oil and gas industry is maintained every five years. Operators in the industry wish that their equipment would last this long: because of the punishing conditions and extreme environment, servicing is required long before the five-year period is up. Most often, after a few years only an overhaul is needed.
SKF has optimized a number of its products to make them appropriate for use in the oil and gas industry. One recent example is an improved tapered roller thrust bearing for top drives, which can help to prolong service intervals and save money.
The top drive – a critical mechanism that forms part of a drilling rig, generates enormous forces. As a consequence, the main internal thrust bearings must withstand extreme conditions: high shock loads, axial loads and possible shaft and housing deflections. At the same time, the combination of heavy loads and low speeds at extreme temperatures pushes the lubrication conditions to the limit –leading to faster wear.
SKF’s redesigned tapered roller thrust bearings can better overcome the above problems, helping to improve the performance and reliability of top drives. This is all the more important, considering that drill rigs are drilling deeper than ever before, putting higher demands on the equipment. One of the main causes of failure is excessive shock loads on the gearbox – and that is what the new bearing is designed to resist.
Outward appearance
There is no outward difference in the bearing’s appearance. In fact, it will look very similar to many competitive products. However, the devil is in the detail: advanced simulation helped SKF to fine-tune the internal geometry, giving the bearing the highest possible load rating.
One element is a new cage design. Using a pin-type cage – rather than a standard brass cage – allows more rollers to fit within the bearing, and thus withstand a greater load. That said, many customers will be fine with a brass cage – as the pin-type cage will be for extreme applications.
Other key design changes include optimising the logarithmic profile, which balances load distribution along each roller. At the same time, rollers are designed to be virtually identical to one another – reducing stress peaks on single rollers, as well as cutting noise and vibration.
While design changes were the key factor behind the performance of the new bearing, some manufacturing changes were also crucial. Enhancing the surface finish by using a different type of coating can help the bearing withstand the effect of marginal lubrication in extreme operating conditions. Drilling often takes place at -40 degrees C (-40F), which can cause the lubricant to thicken. This, combined with high loads, can affect correct lubrication – leading to bearing damage. The advanced surface finish maximizes the effect of the lubricant, reducing excessive friction and damage to the bearing contacts.
It’s important to note that the improved performance is achieved using standard quality SKF steel. For similar performance improvements, competitors are forced to use enhanced material specifications.
SKF has spent significant amount of time developing the new bearing design. It began by analysing SKF bearings that had been used in the field, in an attempt to understand – and overcome – any wear patterns that it found on them. Later, improved designs were modelled using simulation software. The optimized and improved design was validated by simulation tools and field tests.
In addition to these new tapered roller thrust bearings, SKF will showcase two other important bearing innovations at OTC 2016: Kaydon slewing ring bearings; and a sensor bearing unit. Both are appropriate for use in top drives.
Its Kaydon slewing ring bearings can be used in the pipe handling system that is fixed to the bottom of the gearbox of the top drive. Many OEMs save money by making a ‘tailor made’ version using a standard bearing and adding some tooth gears. A better solution is to use a slewing ring bearing with integrated gear, which can help cut failures in the pipe handler.
At the same time, its sensor bearing unit can be used in the top drive’s motor. The product was originally used in the railway industry, but has been adapted for oil and gas – including a version for top drives.. The single unit replaces a bearing and an encoder – and is thus more compact and robust.
Top drives are a critical part of any oil and gas operation, and anything that can improve them – such as these bearing innovations – will help to cut downtime and boost reliability.
Aktiebolaget SKF
(publ)
For further information, please contact:
Press Relations: Nia Kihlström, +46 31-337 2897; +46 706 67 28 97; nia.kihlstrom@skf.com
SKF is a leading global supplier of bearings, seals, mechatronics, lubrication systems, and services which include technical support, maintenance and reliability services, engineering consulting and training. SKF is represented in more than 130 countries and has around 17,000 distributor locations worldwide. Annual sales in 2015 were SEK 75 997 million and the number of employees was 46 635. www.skf.com
® SKF is a registered trademark of the SKF Group.